Co-op Powertrain Engineer
​
Driveline and HEV Engineering - Team
Industrial Projects
DESIGN AND ANALYSIS OF WORK HOLDING DEVICE FOR MILLING OPERATION ON FRONT AXLE BEAM (HCV).
COMPANY-SPONSORED:- BHARAT FORGE LTD.
Description:
-
It is a Bharat Forge company-sponsored project based in Mundva Pune. As problem on SPM machine where milling was done on KP top face of front axle beam was going Out of tolerance due to improper mounting of Axle beam on holding bench.
-
So we designed a Locator which holds the beam in the proper position and minimizes vibration and error with zero tolerance.
The design was within safety limits and increase production.
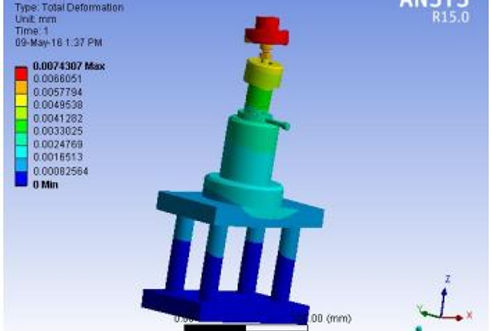
Surface Modeling of Front panel design for heavy duty vehicle
-
The purpose of the project is to model the front outer body design of a Heavy vehicle, step involves where to scan and reverse modeling on scan data to create a class A surface for manufacturing purposes
-
Created an Exterior surface Model of a Heavy Truck using tools like Catia V5 and Imageware CAS (Computer Aided Styling)
-
3D Scan the entire panel using Creaform red light Scanner exported .stl model, Further Aline the model with PLP(Plane line point) technique for building surface.
-
Used CAS class A technique and reverse engineering idea to deliver the design the Client.
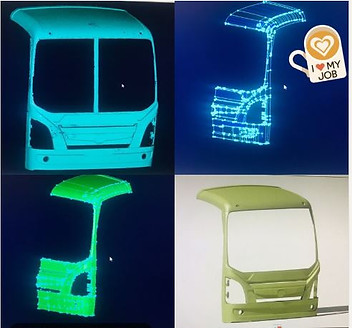
Cutting Tool Development
-
The tool was tempered and ordering the new device was investing more money and time
-
So I scanned the part with a 3D red light scanner and converted it into .stl point cloud data
-
Aline the part in design software with left and point line point (pl) alinements.
-
I started creating surfaces, stitched all covers, and filled the material in CATIA.
-
Then, perform a secondary fillet process and GD&T drawing for the manufacturing team.

3D Scanning (.stl)
-
3D Scanning of the shaft with point pair stich process
Using creaform scanner with verisurf software support -
File exported in .stl formate, used in modeling
and 3D Printing. -
Scan data is used for developing the CADD model and CADD Comparision for quality inspection​

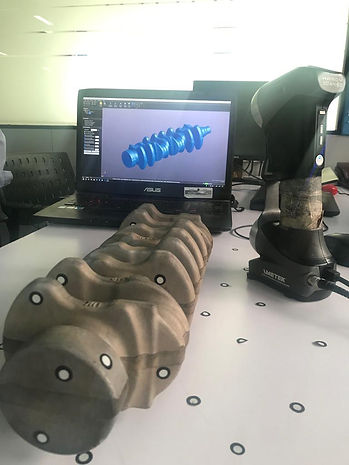
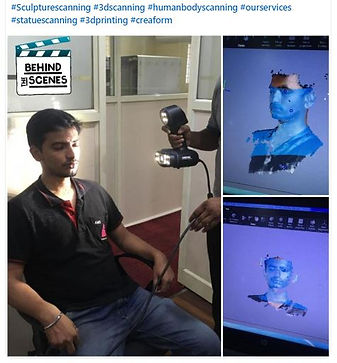

Product Development
Clutch plates of HEV
-
Develop a CADD model of Cluth plates installed in HEV vehicles
-
The procedure was scanning for reference and building a surface model to create a Model for manufacturing
-
Skilled in 3D printing models for aesthetic and adaptive manufacturing in cost-saving and reducing weight
3D Printing (Adaptive Manufacturing)



Other Projects
Some other projects related to 3D quality inspection and CAD comparison of stl with stp , There also some Matlab simulation projects
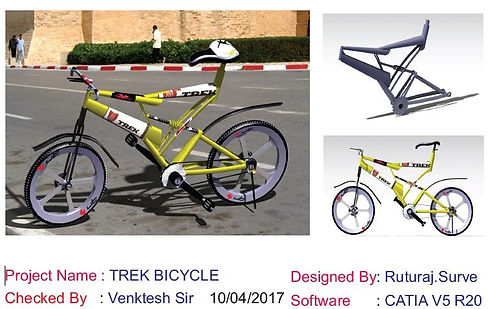
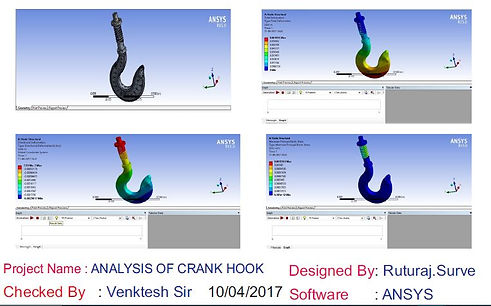